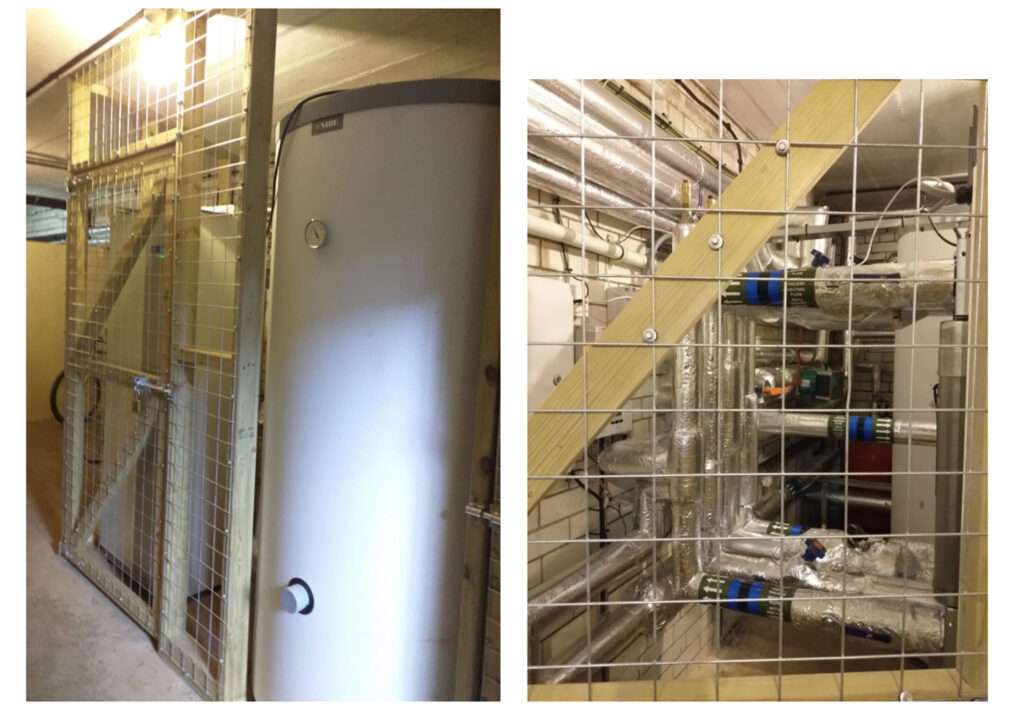
Heat Pump System
Background
Prior to the heat pump installation, the heating system comprised a central boiler plant with three 110kW oil-fired boilers and hot water distribution system to each flat to supply radiators and indirect coils within hot water cylinders. The hot water cylinders also had immersion heaters. The centralised system was operated only in the heating season and was timed to provide heat typically between the hours of 0630 and 0930 and 1830 and 2300 on weekdays and between 0630 and 2300 at weekends. The heating system dates from the late 1970s.
Heat is metered at each property and residents pay for heat on the basis of heat used, in addition to a standing charge to cover fixed costs.
The age of the system and the recent increase in the price of oil together with dissatisfaction in the restricted times of operation motivated the assessment of alternatives. An important consideration is the long-term sustainability of a solution and its impact on climate change.
The Government has set up the Renewable Heat Incentive (RHI) scheme administered by Ofgem to encourage investments in renewable heating systems such as heat pumps and biomass boilers. The level of support varies with scale and the type of technology. The scheme was set to finish in March 2021 and available for projects installed during 2020.
The heating study, conducted with a heating consultant clearly showed that the heat pump solution, and specifically a ground source solution using the “heat” of the lake, was the best in life-cycle cost and in environmental impact. The second best was electric heating using Economy 7, this then moving away from the central system.
System and Procurement Solution
The Ofgem subsidy scheme was used to obtain financing for the installation, with the subsidies being applied to effectively “fund” the installation in most part. The heat usage estimates gave a level of subsidy, which then dictated the capital cost contribution from the financing. This effectively limited the size of the heat pump and heat output, which was sufficient for most of the year except the peak cold periods. The solution was to retain the oil boilers and configure them for backup and supplementary heat supply.
The existing heat distribution was retained with the main supply coming from the heat pump system, and the boilers switched into the supply line when extra heat is demanded.
The total system implementation then consisted of the new heat pump with reticulation to the heat collector coils in the lake, the various electromechanical valves control the flow, a new circulation pump to control the rate of flow through the house, the associated heat and electricity meters. In addition, the heat meters in all flats are being replaced with the latest technology meters which allow distant reading by radio. The cost of this and the meter related plumbing cost were included in the overall budget.
The arrangement with the financing company is that they supply the heat pump system free of charge in exchange for receiving the subsidies, with some extras paid for by the house and a cost basis for over or under heat usage. Put simply, if the heat usage target is not met, the house reimburses the financing company with the shortfall, and if the target is exceeded, the excess subsidy is paid to the house.
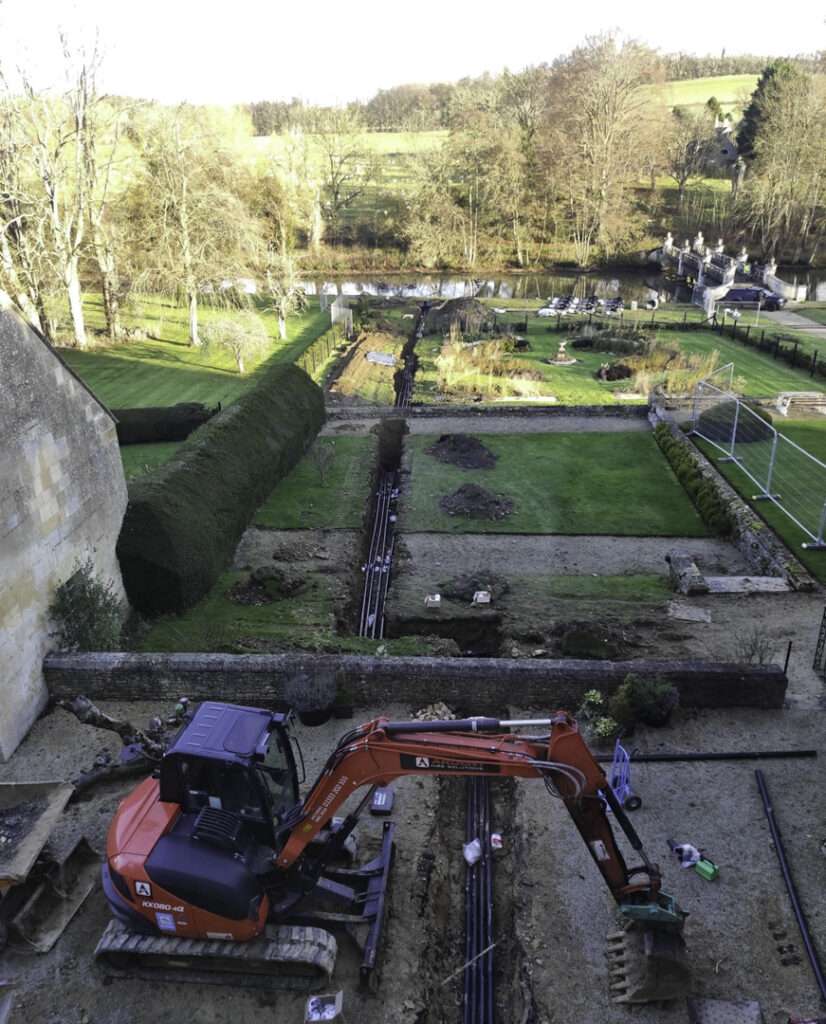
Trenching and supply pipework.
Heat Pump Installation
The installation comprised mainly two parts:
1. The basement installed heat pump with heat storage tank, pressure vessel, brine pump, various valves and integral controller.
2. The collector pipe network in the lake to exchange heat, and associated piping and trenching
In addition there are electrical connections, the fitment of a variable speed main pump, meters, internet connections and even wifi for wifi calling by engineers in order to interact online with the system.
The photos show the work in progress on the trenching, collector preparations, even the tricky negotiation of the old walls and pipes.
With the heat pump being installed in the general basement area there are valves and other controls that are sensitive to interference, therefore a cage to enclose the installation wasconstructed.
Heat Meters
The new heat meters are being installed, with only a few flats still to be done. These will allow the radio link readings using a portable USB reader connected to a battery pack. The USB is then downloaded and data calculated using proprietary software provided by the meter manufacturer, Kamstrup. This allows us to reconcile data for accurate and up to date assessment of heat usage, projected usage and cost accounting. Included is a photo of the heat meter (left), as installed in one of the flats.
System Optimization
This is a key process, as the interplay between the heat pump and the extra boiler heat supply to supplement the heat affects the overall efficiency of the system. Any excess heat by the boilers reduces the heat pump heat and therefore the subsidy from Ofgem. The system was switched on in February 2021 during peak cold conditions, and the optimization and fine tuning of the heat pump settings were not finished by the time the cold peak passed. The optimization will therefore continue during the Winter of 2021/22.
Johan Pretorious
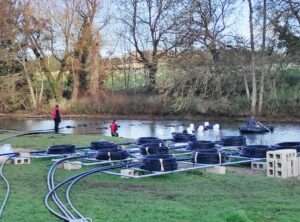
Heat exchanger coils ready for immersion in the lake.
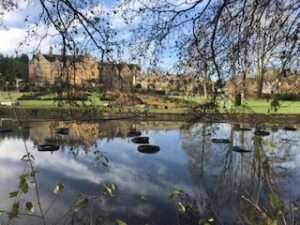
The lake level was lowered to assist in the process.
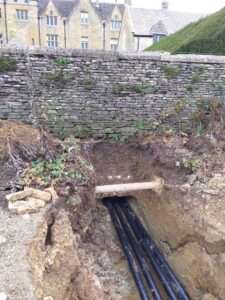
Negotiating the terrace wall.
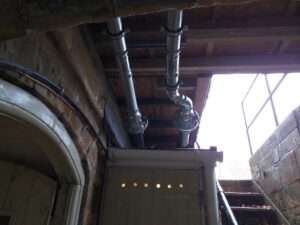
Pipework above the old boiler house door.
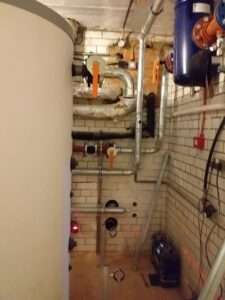
Basement pipework and controls.
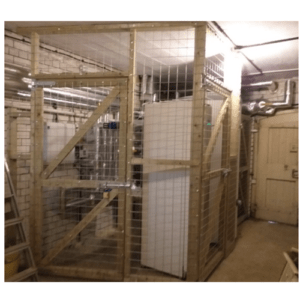
Heat pump enclosure.